-
Maschinen
Hauptmenü
-
Vertikale Fräsmaschinen
Vertikale FräsmaschinenVertikale Fräsmaschinen Alles anzeigen
- Vertikale Fräsmaschinen
- VF-Baureihe
- Universalmaschinen
- VR Serie
- VP-5 Prismatisch
- VMCs mit Palettenwechsler
- MiniMill
- Formenbaumaschinen
- Hochgeschwindigkeits-Bohrzentren
- Bohren/Gewindebohren/Fräsmaschinen
- Werkzeug- und Vorrichtungsbau
- Kompaktfräsmaschinen
- Portal-Baureihe
- SR Blatt-Router
- Extra große VMC
- Doppelständer-Fräsmaschinen
- Steuerungssimulator
- Taschenfräsen
- Automatischer Werkstücklader für Fräsen
- VMC/UMC Seitenlader Automatischer Werkstücklader
- Kompakter automatischer Werkstücklader
-
Mehrachsen-Lösungen
Mehrachsen-LösungenMehrachsen-Lösungen Alles anzeigen
-
Drehmaschinen
DrehmaschinenDrehmaschinen Alles anzeigen
-
Horizontale Fräsmaschinen
Horizontale FräsmaschinenHorizontale Fräsmaschinen Alles anzeigen
-
Dreh- und Indexiertische
Dreh- und IndexiertischeDreh- und Indexiertische Alles anzeigen
-
Automatisierungssysteme
AutomatisierungssystemeAutomatisierungssysteme Alles anzeigen
-
Tischmaschinen
TischmaschinenTischmaschinen Alles anzeigen
-
Werkstattausrüstattung
WerkstattausrüstattungWerkstattausrüstattung Alles anzeigen
-
Taschenmaschinen
TaschenmaschinenTaschenmaschinen Alles anzeigen
EINKAUFSINFORMATIONENMÖCHTEN SIE MIT JEMANDEM SPRECHEN?Ihr Haas-Händler (Haas Factory Outlet, HFO) kann Ihre Fragen beantworten und Sie durch die besten Varianten führen.
CONTACT YOUR DISTRIBUTOR > -
Vertikale Fräsmaschinen
-
Sonderzubehör
Hauptmenü
-
Spindeln
SpindelnSpindeln Alles anzeigen -
Werkzeugwechsler
WerkzeugwechslerWerkzeugwechsler Alles anzeigen -
4- | 5-Achsen
4- | 5-Achsen4- | 5-Achsen Alles anzeigen -
Revolver und angetriebene Werkzeuge
Revolver und angetriebene WerkzeugeRevolver und angetriebene Werkzeuge Alles anzeigen -
Messtasten
MesstastenMesstasten Alles anzeigen -
Späneabfuhr- und Kühlmittelverwaltung
Späneabfuhr- und KühlmittelverwaltungSpäneabfuhr- und Kühlmittelverwaltung Alles anzeigen -
Die Haas Steuerung
Die Haas SteuerungDie Haas Steuerung Alles anzeigen -
Produktoptionen
ProduktoptionenProduktoptionen Alles anzeigen -
Werkzeuge und Spannvorrichtungen
Werkzeuge und SpannvorrichtungenWerkzeuge und Spannvorrichtungen Alles anzeigen -
Werkstückhalterung
WerkstückhalterungWerkstückhalterung Alles anzeigen -
5-Achsen-Lösungen
5-Achsen-Lösungen5-Achsen-Lösungen Alles anzeigen -
Automatisierung
AutomatisierungAutomatisierung Alles anzeigen
EINKAUFSINFORMATIONENMÖCHTEN SIE MIT JEMANDEM SPRECHEN?Ihr Haas-Händler (Haas Factory Outlet, HFO) kann Ihre Fragen beantworten und Sie durch die besten Varianten führen.
CONTACT YOUR DISTRIBUTOR > -
-
Why Haas
Hauptmenü
Entdecken Sie den Haas Unterschied
-
Service
Hauptmenü
Willkommen bei Haas Service
- Videos Hauptmenü
-
Haas Werkzeuge
Hauptmenü
- Haas Werkzeuge
-
Winner's CircleWinner's Circle Shop All
-
Winner's CircleWinner's Circle Shop All
-
Heutige SchnäppchenHeutige Schnäppchen Shop All
- Fräsen-Werkzeughalter
- Fräswerkzeuge
- Mess- und Prüfwerkzeuge
- Bohrsysteme
- Werkstückhalterung für Fräsen
- Werkzeughaltersätze für Plan- und Eckfräser
- Drehmaschinen-Werkzeugaufnahme
- Werkzeuge für Drehzentren
- Drehmaschine-Werkstückhalterung
- ER Spannhülsen und Spannfutter
- Bohren
- Gewindedrehen
- Räumen
- Werkzeuglagerung
- Bekleidung und Zubehör
-
AusverkaufAusverkauf Shop All
-
Mess- und PrüfwerkzeugeMess- und Prüfwerkzeuge Shop All
- Messtaster-Sätze und Zubehör
- Kanten- und Mittentaster
- Vergleichsmessgeräte
- Höhenmessgeräte
- Bremszangen
- Stopfen- und Ringmessgeräte
- Messblöcke und Zubehör
- Messstifte und Zubehör
- Messuhr mit Taststift
- Prüfhebelmessgeräte
- Bohrungsmessgerät
- Zubehör für Indikatoren
- V-Blöcke
- Einrichtungsblöcke
- Tiefenmessung
- Mikrometer
- Mikrometer Zubehör
- Mikrometer-Sätze
- Bohrungsmessgerät-Sätze
- Startersatz
- Messgeräte-Sätze
- Messschieber-Sätze
- Werkzeugprüfstation
- Höheneinsteller
- Coordinate Measuring Machines
-
Cobots und ZubehörCobots und Zubehör Shop All
-
Shop SupportShop Support Shop All
-
Fräsen-WerkzeughalterFräsen-Werkzeughalter Shop All
-
FräswerkzeugeFräswerkzeuge Shop All
- Fräseraufnahme-Körper
- Frässchneidplatten
- Schaftfräsen
- Phasenfräser und Schneidplatten
- Indexierbare Schaftfräser-Körper
- Kugelschaftfräser
- Phasen-Stirnfräser
- Schruppen (mit Schaftfräser)
- INDX-Kugelfräser und -Wendeschneidplatten
- Werkzeughaltersätze für Plan- und Eckfräser
- Fasenfräsersätze
- Indexierbare Schaftfräsersätze
- Schwalbenschwanzfräser
- Indexierbare Schwalbenschwanzfräser
- Gravur-Schaftfräser
- Grate
- Schlitzfräser
- Schaftfräser zur Eckenabrundung
- CNC-Router-Bits für Holz
-
BohrsystemeBohrsysteme Shop All
-
Werkstückhalterung für FräsenWerkstückhalterung für Fräsen Shop All
- Schraubstöcke mit festen Spannbacken
- Selbstzentrierende Schraubstöcke
- Adapterplatten
- Schraubstock-Spannbacken
- Schraubstockhalterungen und -befestigungen
- Vise Kits
- Schraubstock-Parallelunterlagen
- Drehmaschinen-Schraubstock-Sätze
- Vorrichtung Festklemmen
- Automatisierte Werkstückhalterungssätze
- Schraubstock für Werkzeughersteller
- Messgeräte für die Klemmkraft
- Spannzangenvorrichtungen
- Winkelplatten
-
Drehmaschinen-WerkzeugaufnahmeDrehmaschinen-Werkzeugaufnahme Shop All
-
Werkzeuge für DrehzentrenWerkzeuge für Drehzentren Shop All
- Abstechwerkzeuge
- Abstechwerkzeugsätze
- Drehschneidplatten
- Einstech- und Abstechwerkzeuge
- Interne Einstech- und Gewindewerkzeuge (ID)
- Gewindeeinsatz
- Werkzeuge zum Gewindedrehen
- Bohrstangen / Interne (ID) Drehwerkzeuge
- Externe (OD) Drehwerkzeuge
- Cermet-Wendeschneidplatten
- CBN-Drehwendeschneidplatten
- Haas Wendeschneidplatten zur Bearbeitung von Nuten und für Gewinde
- Haas Werkzeughalter – Bearbeitung von Nuten und Gewindedrehen
- Micro Turning Tools
-
Drehmaschine-WerkstückhalterungDrehmaschine-Werkstückhalterung Shop All
-
PaketsätzePaketsätze Shop All
- SPANLÜFTERSÄTZE
- Schneidwerkzeugsätze
- Indexierbare Schaftfräsersätze
- Abstechwerkzeugsätze
- Gewindebohr- und Bohrsätze
- Indexierbare Bohrsätze
- Werkzeughaltersätze für Plan- und Eckfräser
- Fasenfräsersätze
- Drehtisch-Werkzeughalter und Spannfuttersätze
- 08-1769
- 08-1739
- 08-0002
- 08-1117
- 08-1744
- 08-1118
- 08-0004
- 08-1745
- 08-1748
- 08-1952
- 08-1953
- 08-1954
- 08-1955
- 08-2027
- 08-2028
- 08-2029
- Startersätze für Drehmaschinen
- Werkstückhalterungssätze
- Drehmaschinen-Schraubstock-Sätze
- Vise Kits
- Dreibackenfutter Sätze für Fräsen
- Spannwürfel-Sätze
- Reduzierhülse Sätze
- Automatisierte Werkstückhalterungssätze
- 08-1869
- 08-1870
- Sätze für Messung und Inspektion
- Mikrometer-Sätze
- Bohrungsmessgerät-Sätze
- Startersatz
- Messgeräte-Sätze
- Messschieber-Sätze
-
ER Spannhülsen und SpannfutterER Spannhülsen und Spannfutter Shop All
-
BohrenBohren Shop All
-
GewindedrehenGewindedrehen Shop All
-
RäumenRäumen Shop All
-
SpannwürfelSpannwürfel Shop All
-
Manuelles Spannfutter zum FräsenManuelles Spannfutter zum Fräsen Shop All
-
Entgrat- und SchleifmittelEntgrat- und Schleifmittel Shop All
-
Werkzeug-Voreinstellarm und WärmeschrumpferWerkzeug-Voreinstellarm und Wärmeschrumpfer Shop All
-
WerkzeuglagerungWerkzeuglagerung Shop All
-
MaschinenwartungMaschinenwartung Shop All
-
WerkzeugzubehörWerkzeugzubehör Shop All
- Kegel für Spindel und Werkzeughalter
- Haas Shop Lift
- Werkzeughalter-Befestigungen
- CNC-Gebläse zur Spanentfernung
- Dead Blow Hammers
- Hämmer und Schneidhämmer
- Anti-Fatigue Mats
- Ersatzteile
- Layout Tools
- Schraubenschlüssel
- Handgeführte Schneidwerkzeuge
- Werkzeuge kaufen
- Hubmagnete
- Safety Apparel
- Schärfer für Schneidwerkzeuge
-
Bekleidung und ZubehörBekleidung und Zubehör Shop All
Automatisierungszubehör
Shop Support
Fräsen-Werkzeughalter
Fräsmaschinen-Schneidwerkzeuge
Bohrsysteme
Werkstückhalterung für Fräsen
Drehmaschinen-Werkzeughalter
Drehmaschinen-Schneidwerkzeuge
Drehmaschine-Werkstückhalterung
Paketsätze
ER Spannzangen und Spannfutter
Bohren
Gewindedrehen
Räumen
Spannwürfel und Sätze
Manuelle Spannfutter zum Fräsen
Entgraten und Schleifen
Werkzeug-Voreinstellarm und Wärmeschrumpfer
Aufstellung und Bedienung
Maschinenwartung
Werkzeugzubehör
Bekleidung und Zubehör
Mess- und Prüfwerkzeuge
Winner's Circle
Winner's Circle
Lagerräumung
Hot Deals für heute
HAAS TOOLING QUICK LINKS
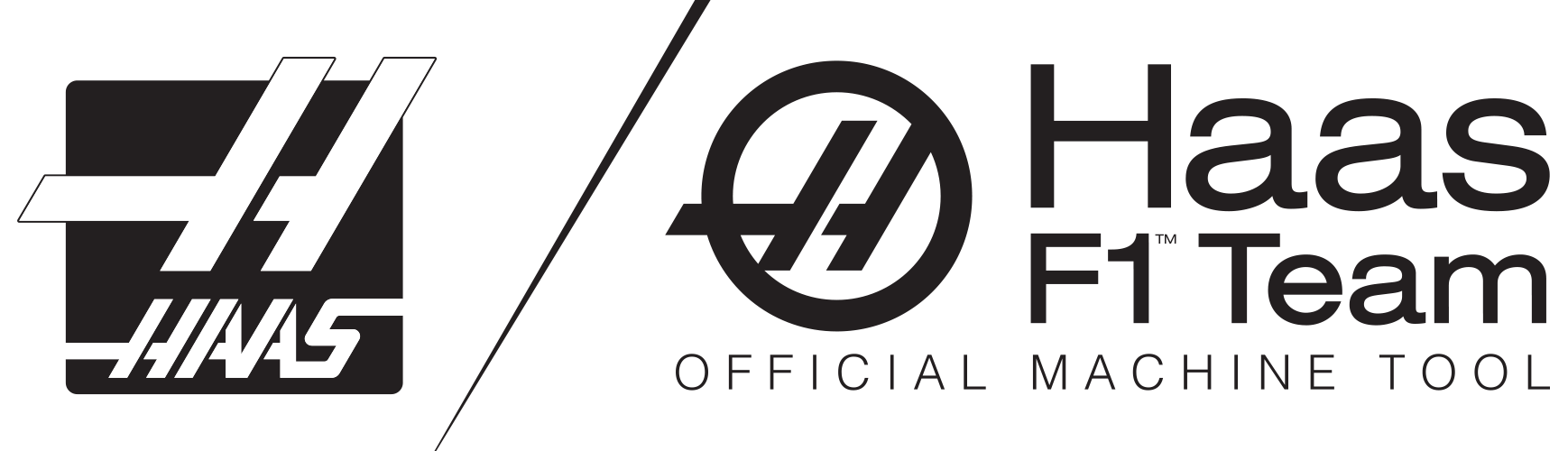